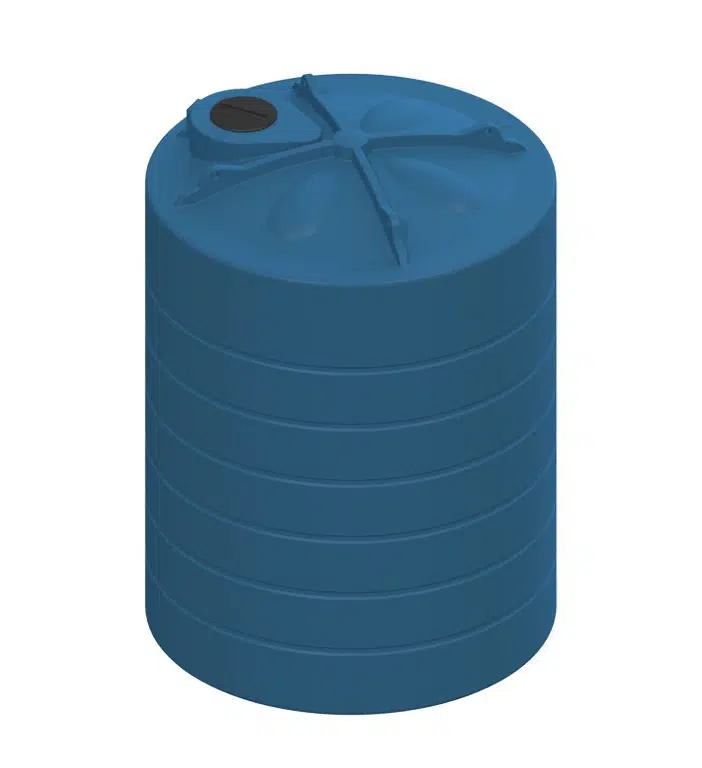
Rotational Moulding
Advantages
- The tooling cost is much lower, making rotational moulding ideal for smaller production runs. Galloway Group uses rotational moulding for cost-effective production runs ranging from a single product to (quantity needed).
- There are virtually no size limitations on the products that can be produced with rotational moulding.
- The rotomoulding process produces an extremely uniform thickness for the product walls, even at the corners, which can be a weak spot with other processes.
- Complex shapes can be included in the moulding process, for handles, threads and graphics. This removes the necessity for secondary processes that would entail extra costs.
- Rotational plastics are renowned for their durability; the material can be UV resistant, colourfast and it will not corrode.
What materials can be used in rotational moulding?
The primary material used is polyethylene, although a range of other materials can be used, including PVC, nylon, polypropylene, cross-linked polyethylene, metallocene polyethylene and plastisols.